11:45 – 16:15 4,5 h – total 1588 h
Bei der Fahrt zur Werkstatt ist mir eingefallen, dass ich schon lange die Seitenleisten, über die man beim Einsteigen die Füße heben muss, mit einer Kunststoffleiste als Schutz versehen wollte. Die Side Skins stehen etwa 1 bis 2 mm über die waagerechten Leisten hervor. Kommt man mit den Schuhen beim Ein- oder Aussteigen in Kontakt, könnte man die Side Skin verbiegen aber zumindest den Lack beschädigen. Dies ist an einigen Stellen schon passiert. Deshalb habe ich mir 3 mm dicke, 30 mm breite Kunststoffleisten gekauft, die ich heute zugeschnitten habe, mit der Feile in die endgültige Form gebracht habe und mit doppelseitigem Klebeband eingefügt habe. Jetzt bin ich zufrieden! Als ich dann mit dem Anfertigen des Doublers für die XPDR-Antenne weitermachen wollte, ist mir aufgefallen, dass das zur Verfügung stehende Material gewitzt verwendet werden sollte, sonst muss ich mir neues bestellen. Ich habe deshalb zuerst die großen Teile für den Boden des E&E-Compartments herausgeschnitten. Anschließend habe ich den Doubler zugeschnitten. Mit einem Blatt Papier und einem Bleistift habe ich den Bereich des Flugzeugbodens „kopiert“, wo die Antenne angeschraubt werden soll. Das Ergebnis habe ich auf das Blech übertragen, die Bohrungen gesetzt und mit dem Edge Forming Tool die Kannten bearbeitet. Die Nieten am Flieger musste ich natürlich ausbohren. Als nächste muss der Doubler grundiert werden, bevor ich ihn einnieten kann. Später muss er dann noch lackiert werden.
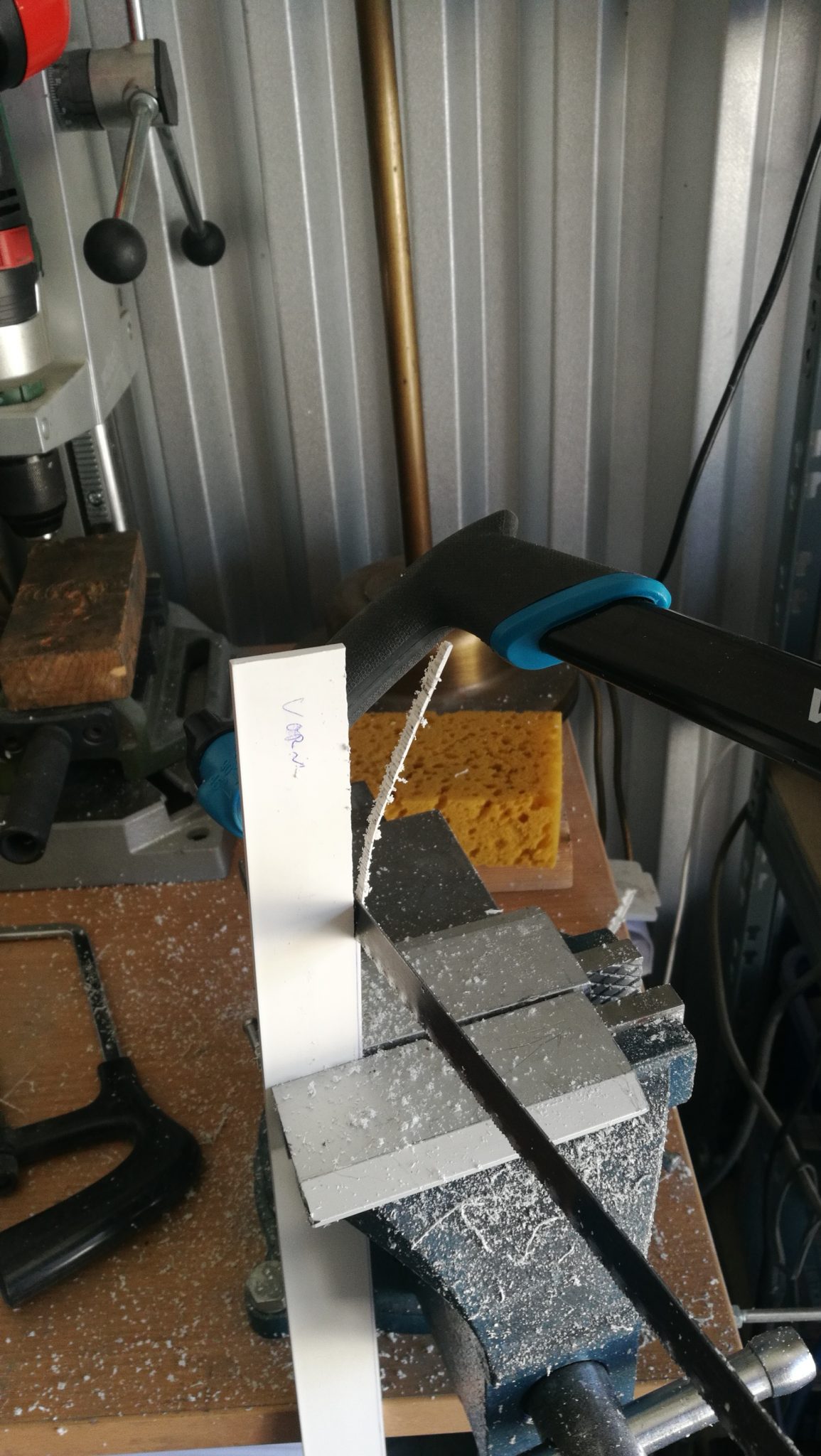
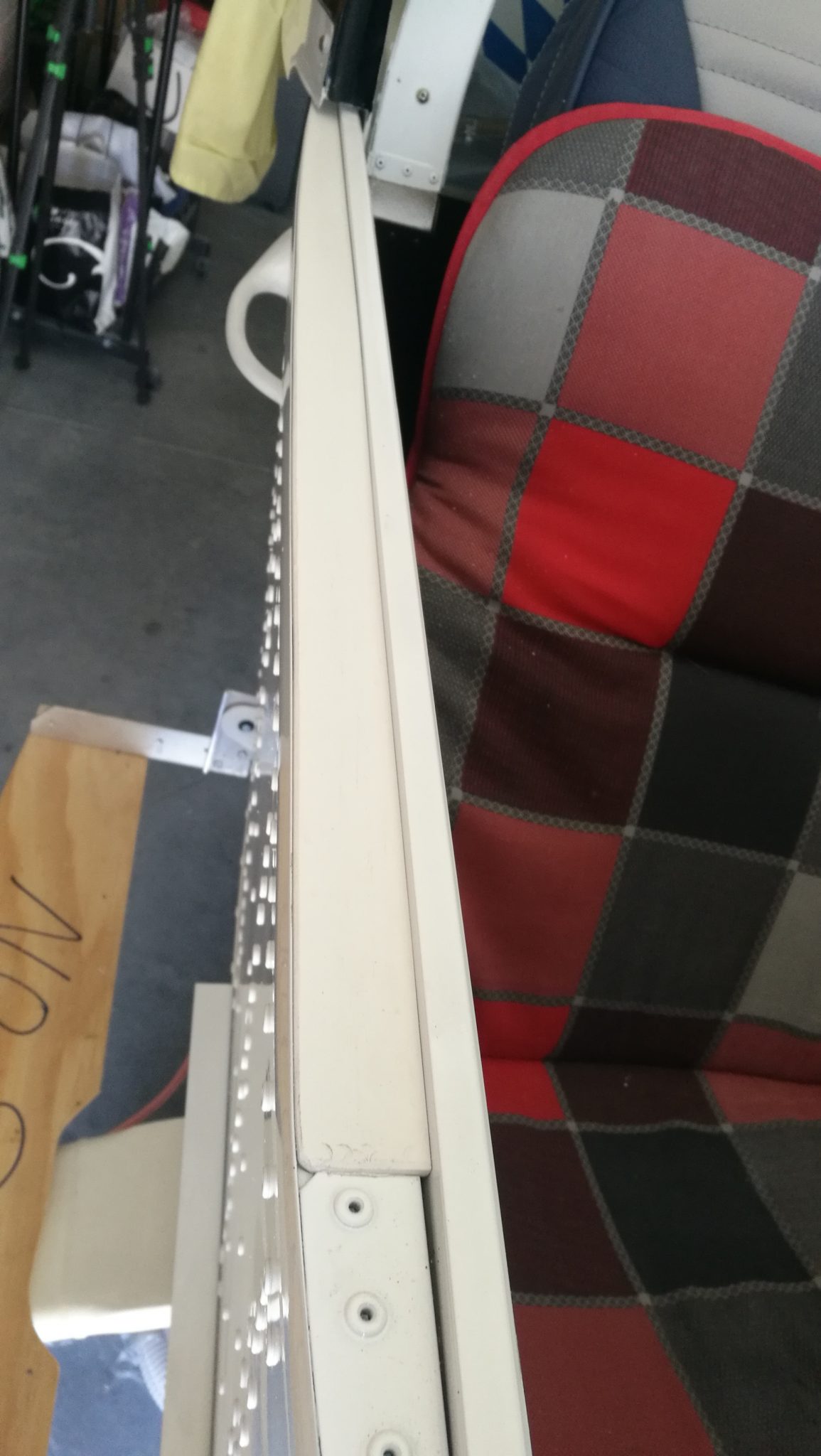
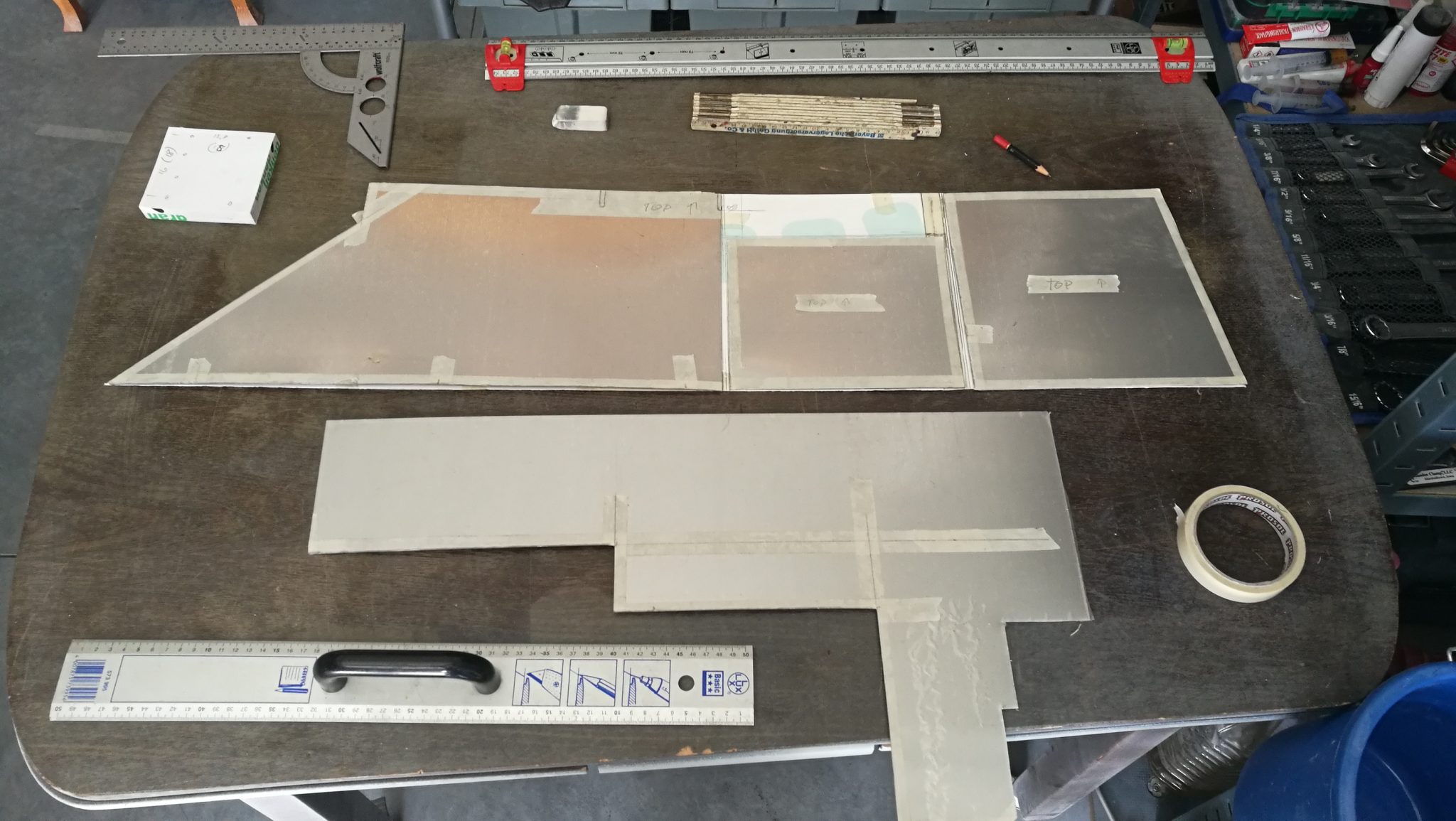
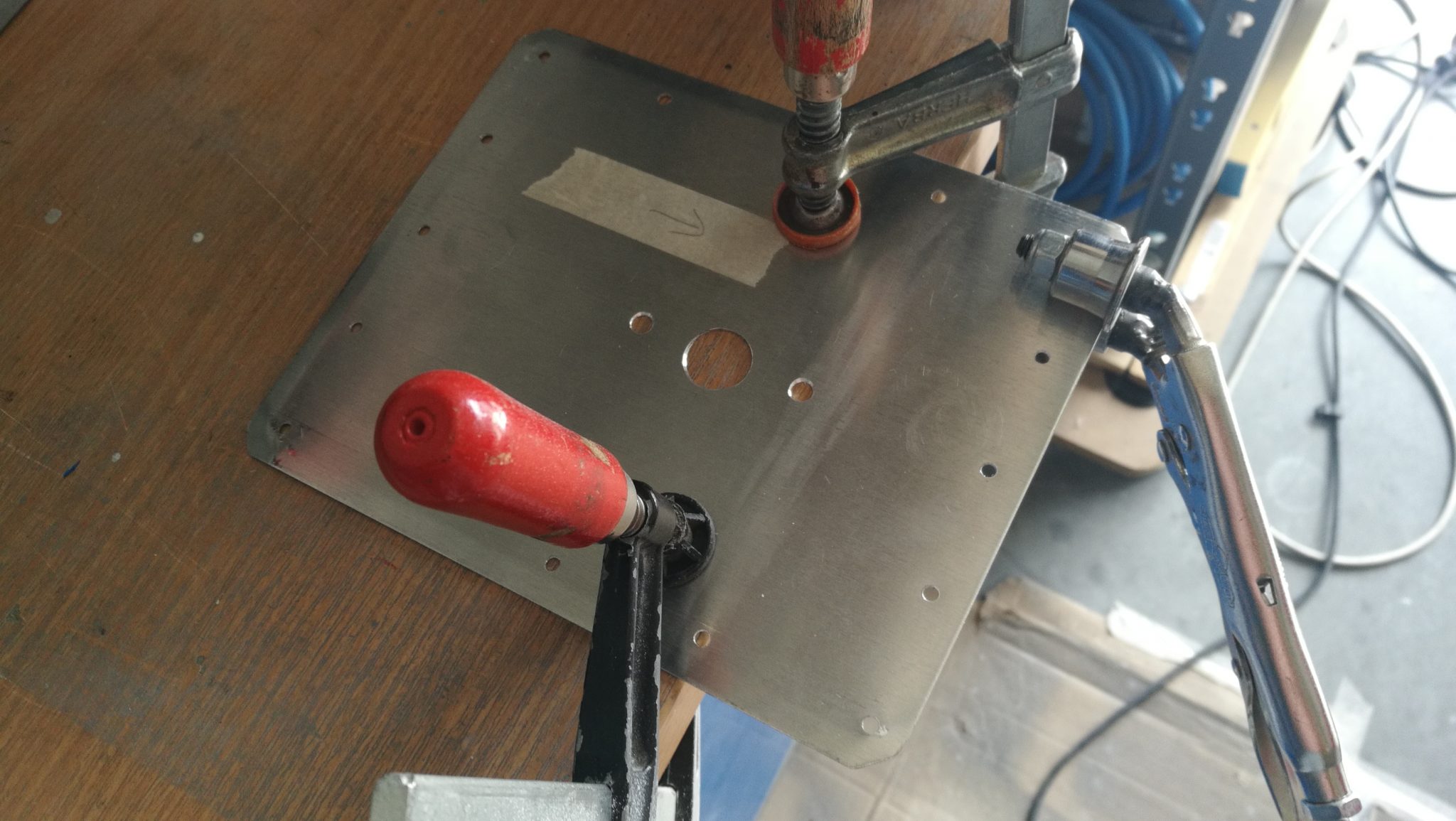
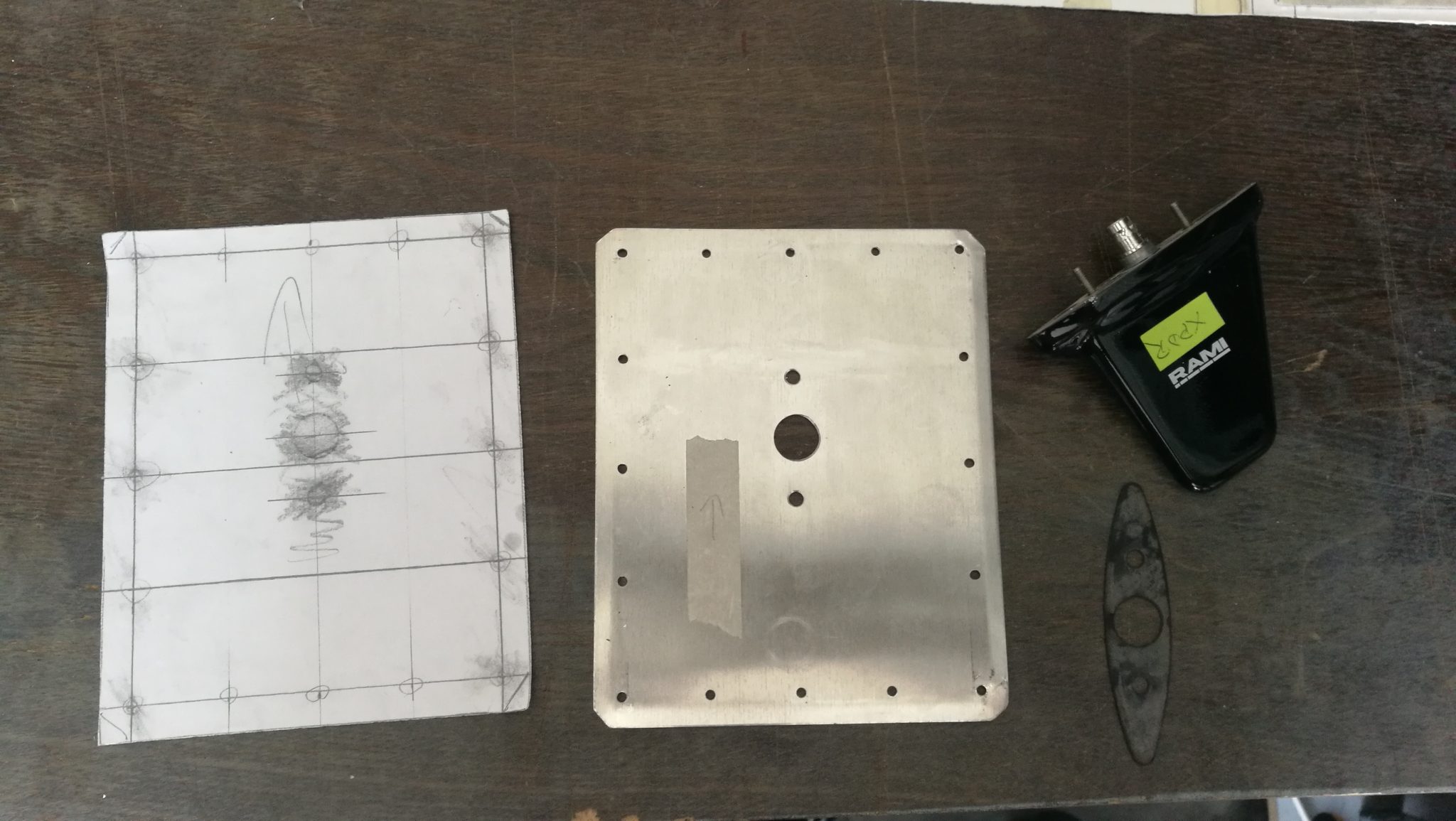
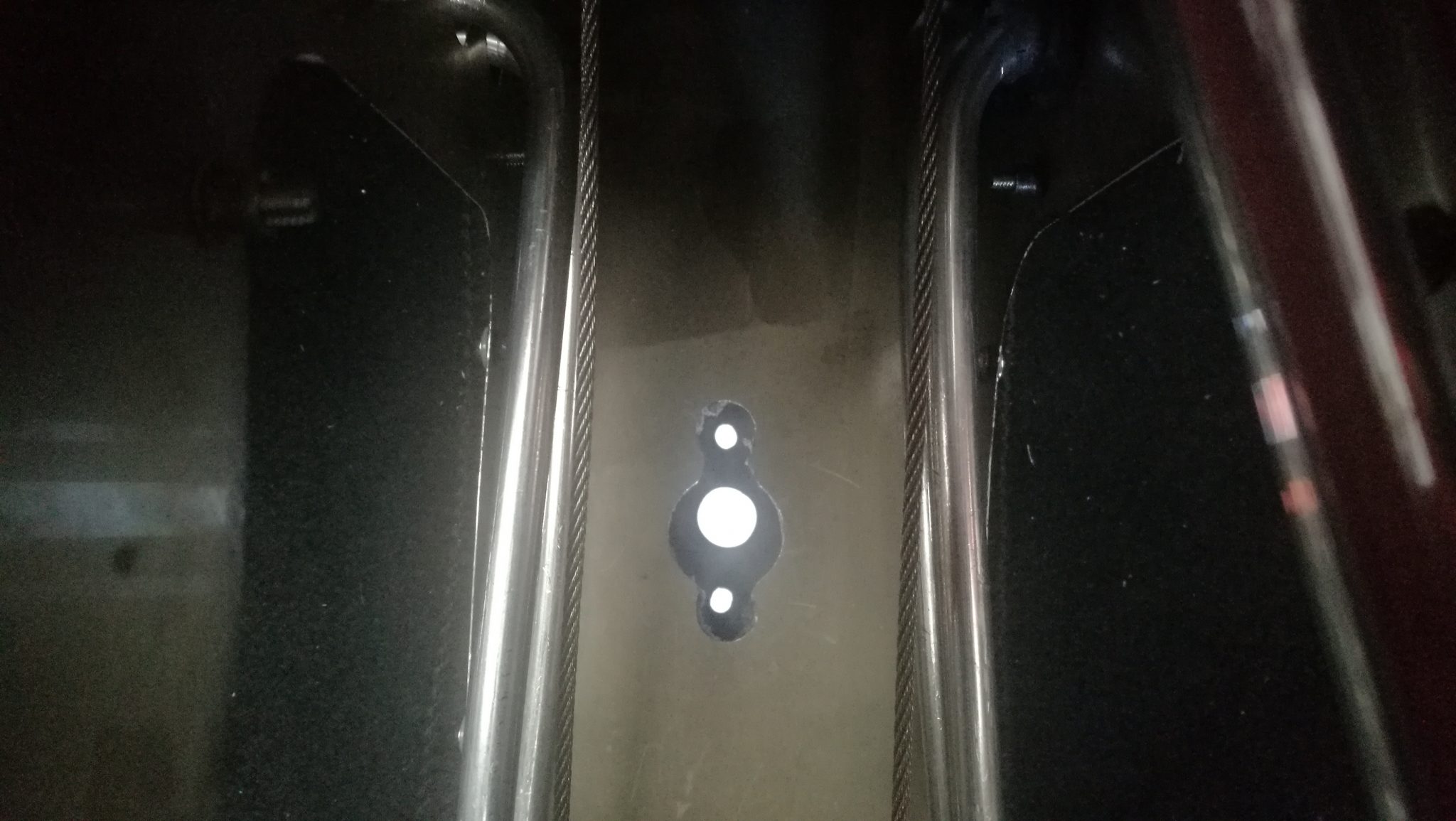
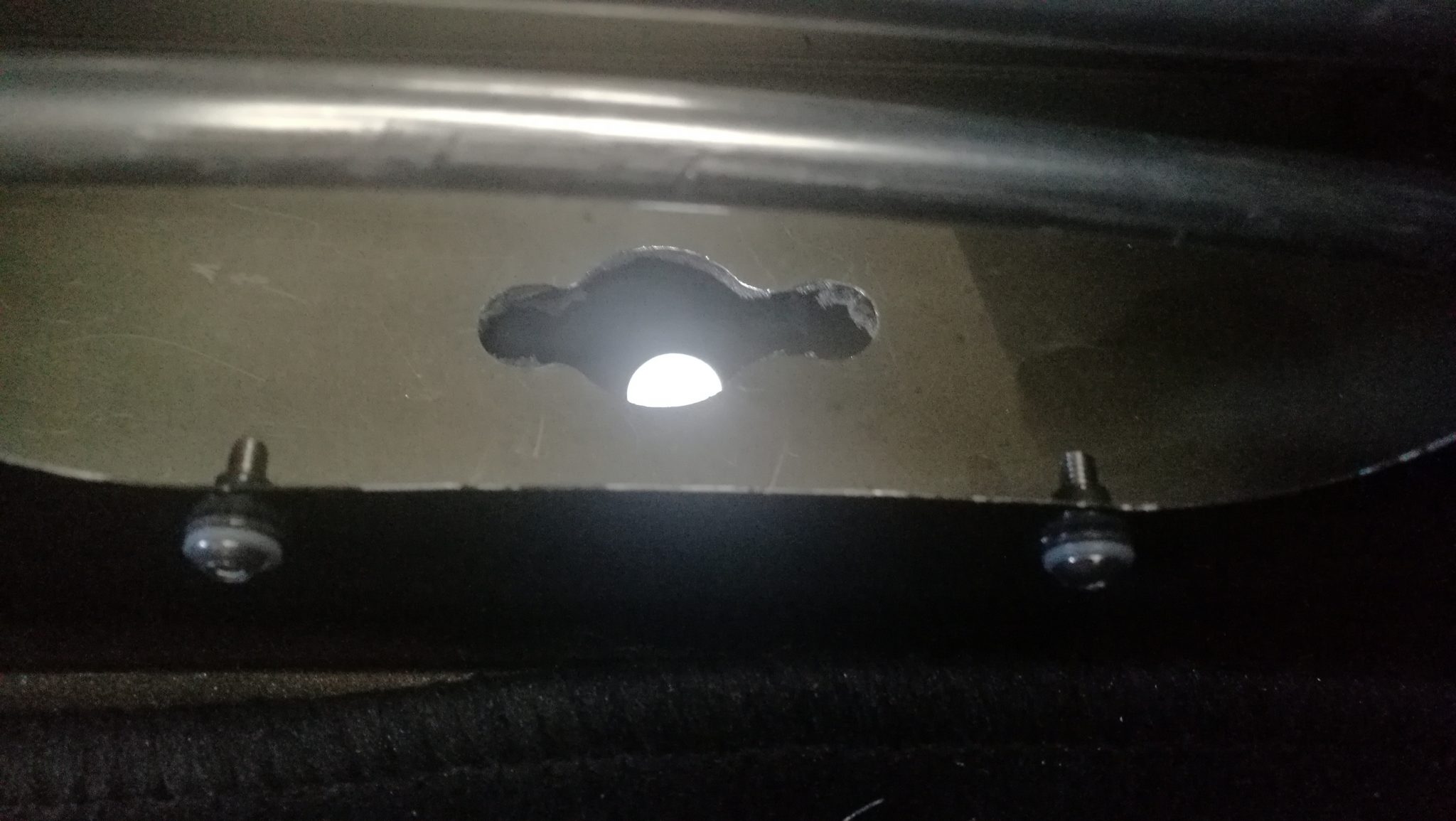
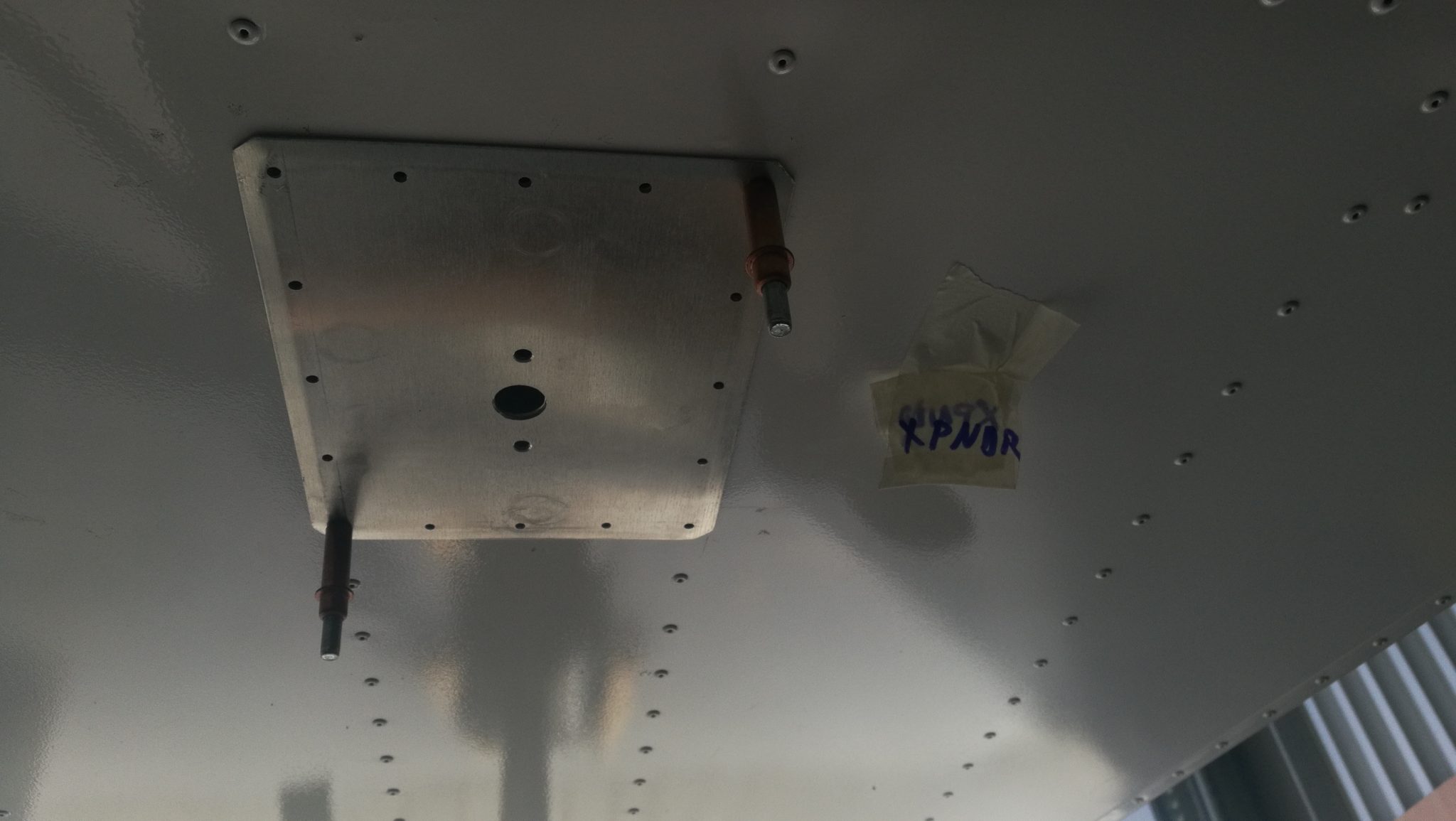