14:00 – 17:00 3 h – total 1449,25 h
Die Durchführung der Fuel Line durch die rechte Side Skin habe ich fertiggestellt. Danach habe ich den provisorischen Tank angeschlossen. Die Positionen der Anschlüsse entsprechen der Wing. Der Filter hat Platz! Anschließend habe ich mir weiter den Kopf zerbrochen, wie ich die Leitungen einerseits im Cockpit verlegen könnte und andererseits im Motorraum. Das Cockpit ist mittlerweile recht klar für mich. Ich werde nochmals Bulkhead-Fittinge am Tunnel anbringen und so die Alu Tubes stabil befestigen. Im Motorraum bin ich mir noch nicht sicher. Ich liebäugle damit, die Auspuffheizung wieder abzubauen. Die heiße Luft wird, wenn man das Cockpit nicht heizen will, genau in die Richtung der Fuel Pums geblasen. Ich glaube nicht dass das gut ist. Nachdem ich eine Wasser-Cockpit-Heizung installiert habe, braucht es die Auspuffheizung gar nicht mehr. Ich wollte nur die unterschiedliche Wirkungsweise austesten. Aber so wichtig ist mir das auch nicht und ich spare mir noch einen Bowdenzug zur Klappensteuerung.
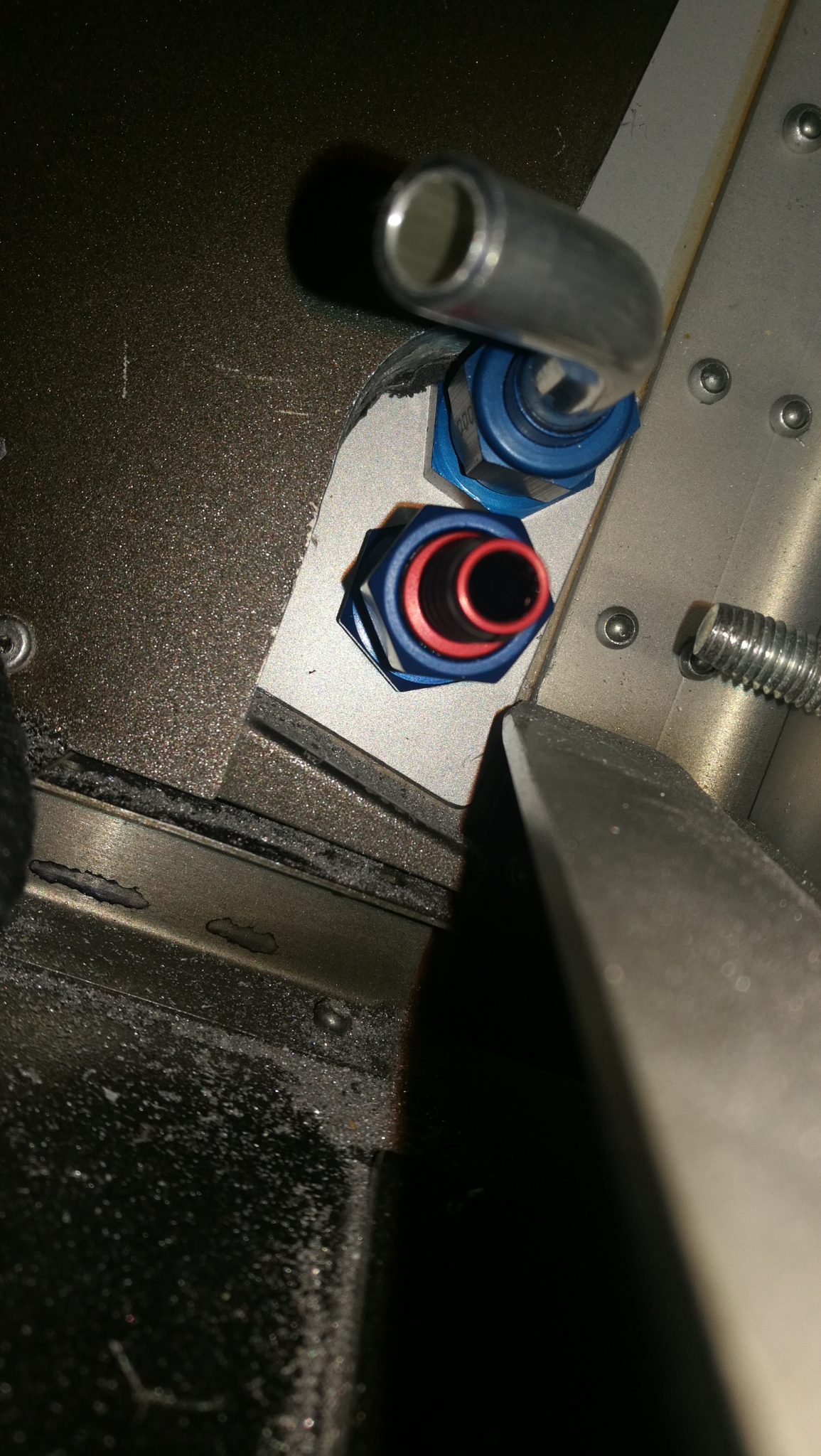
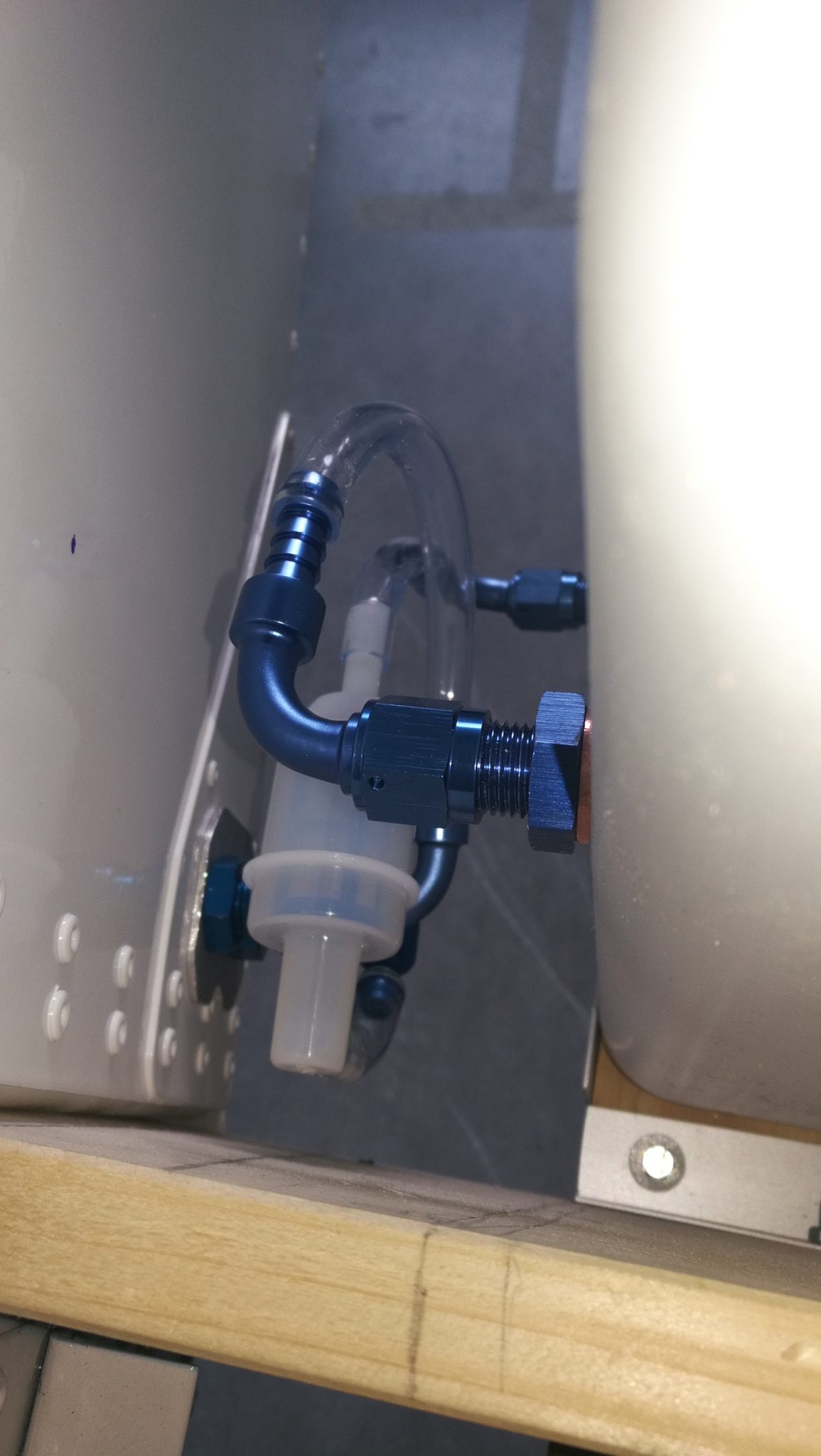
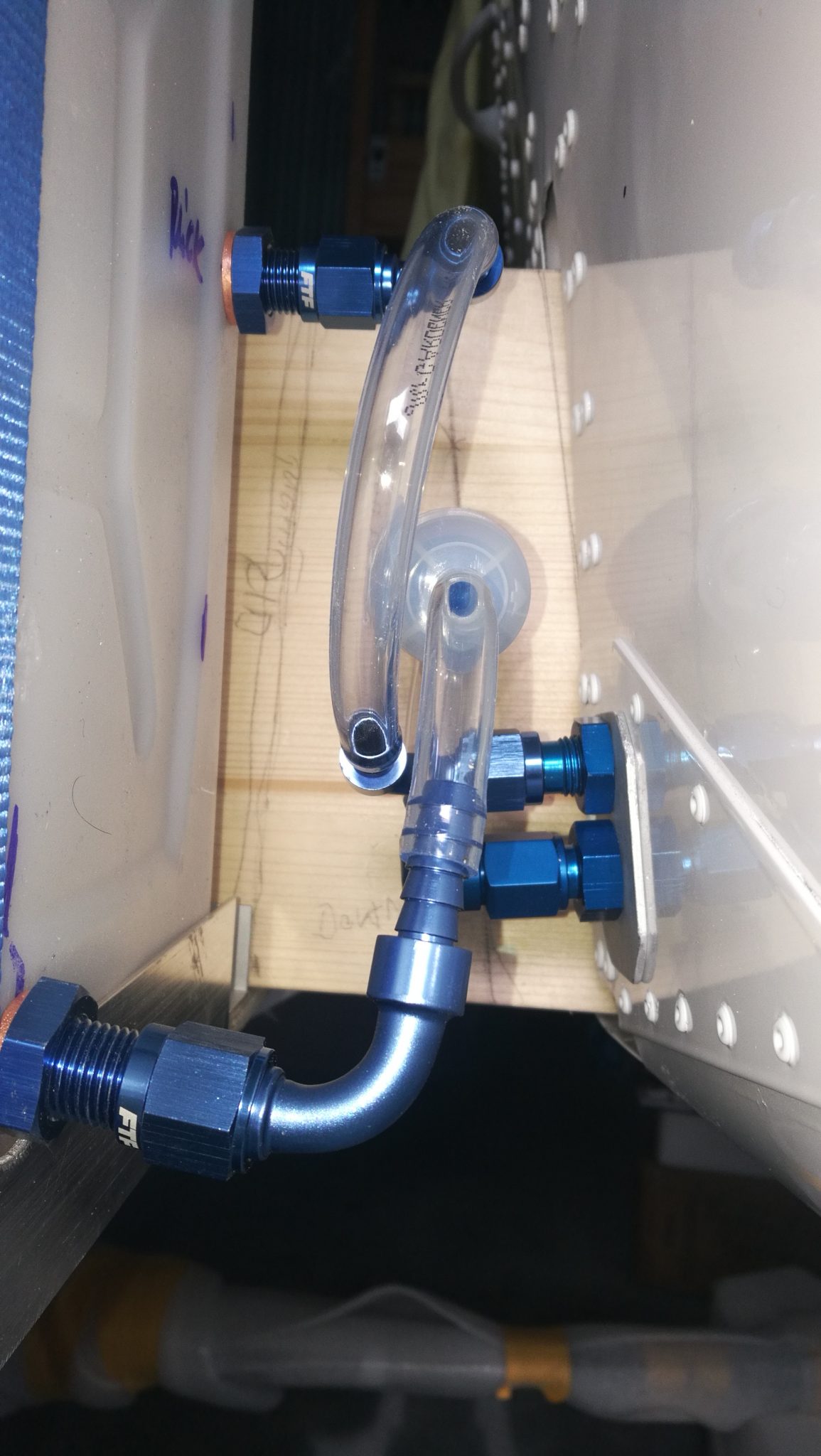
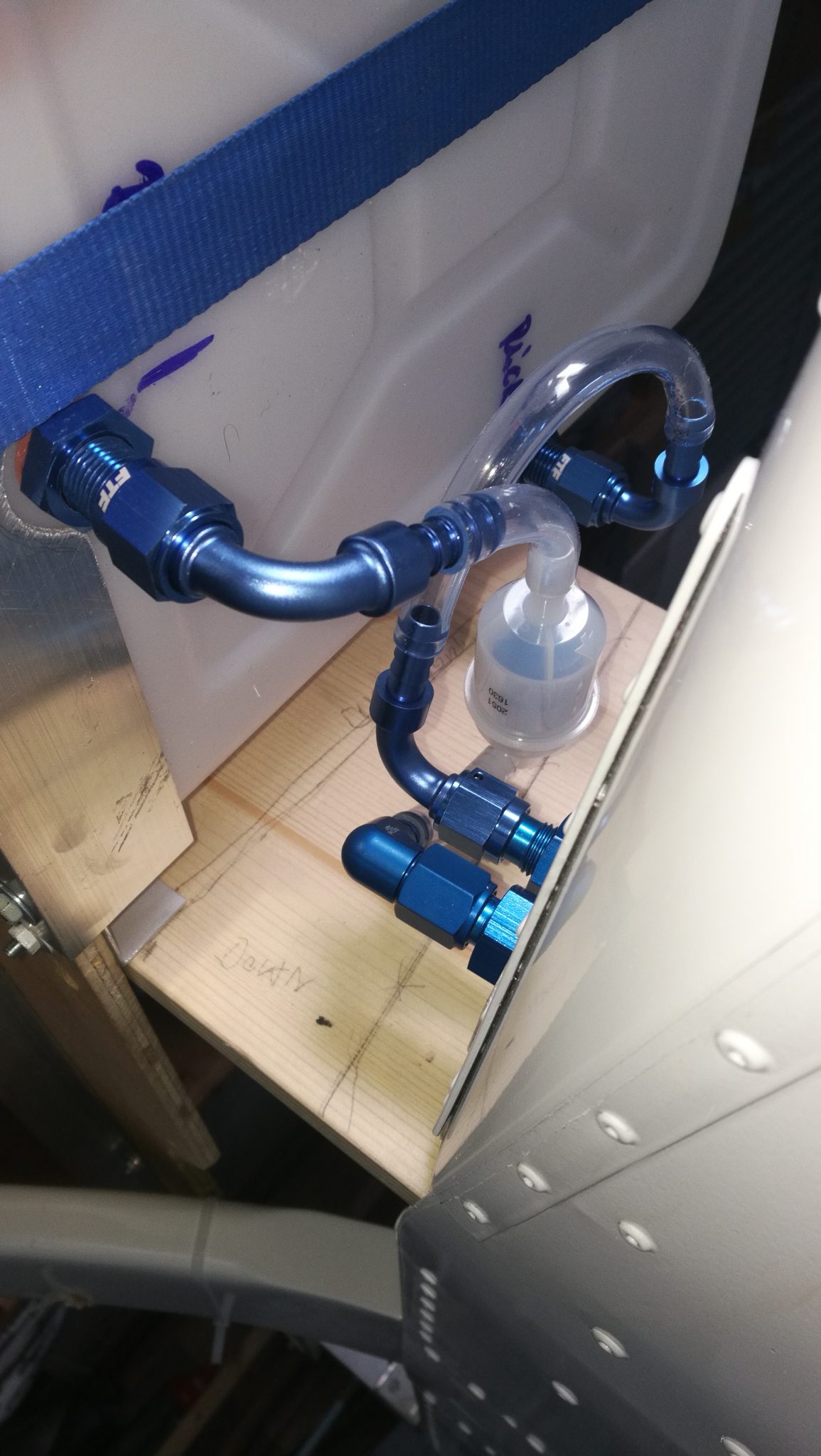
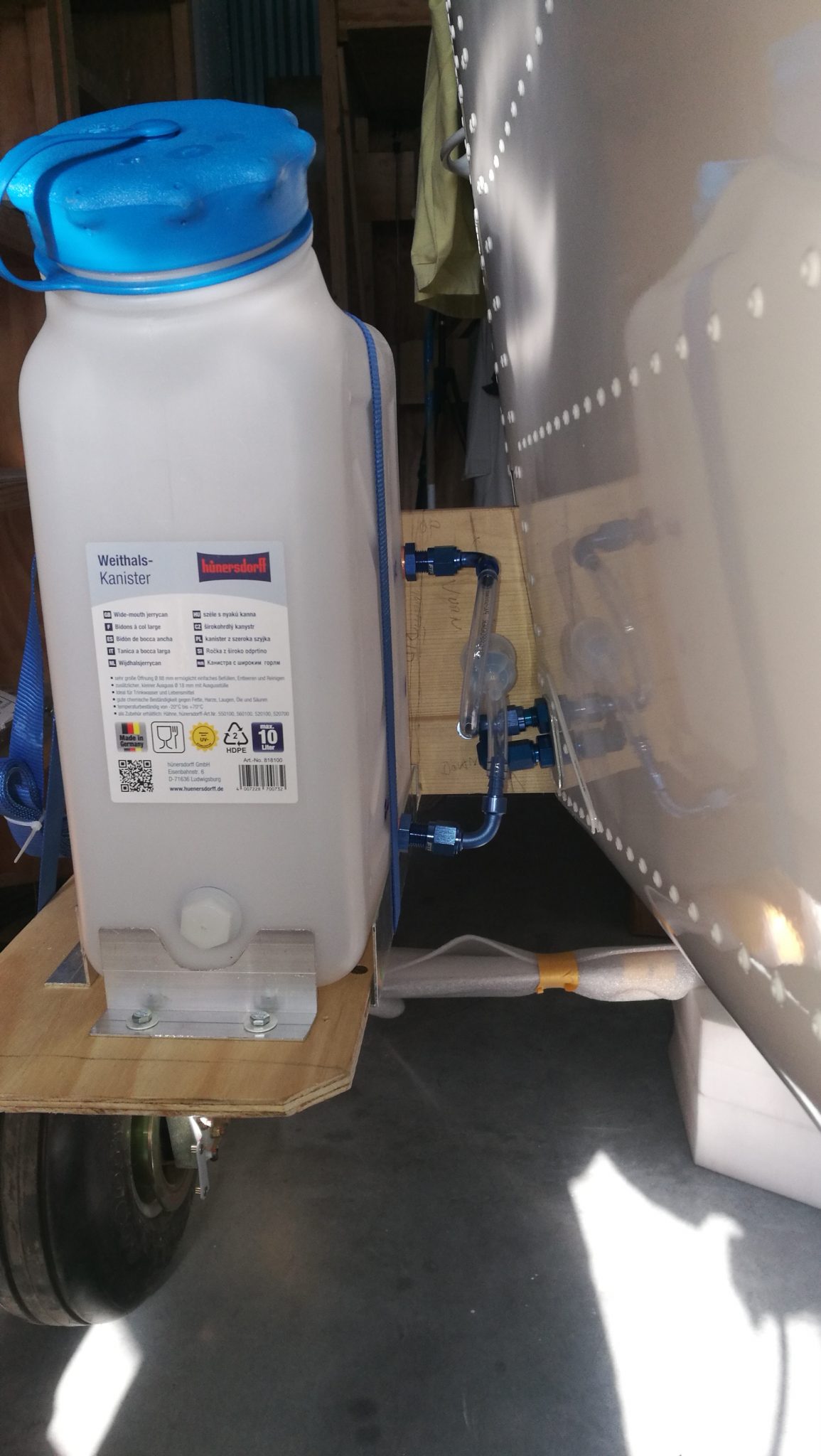
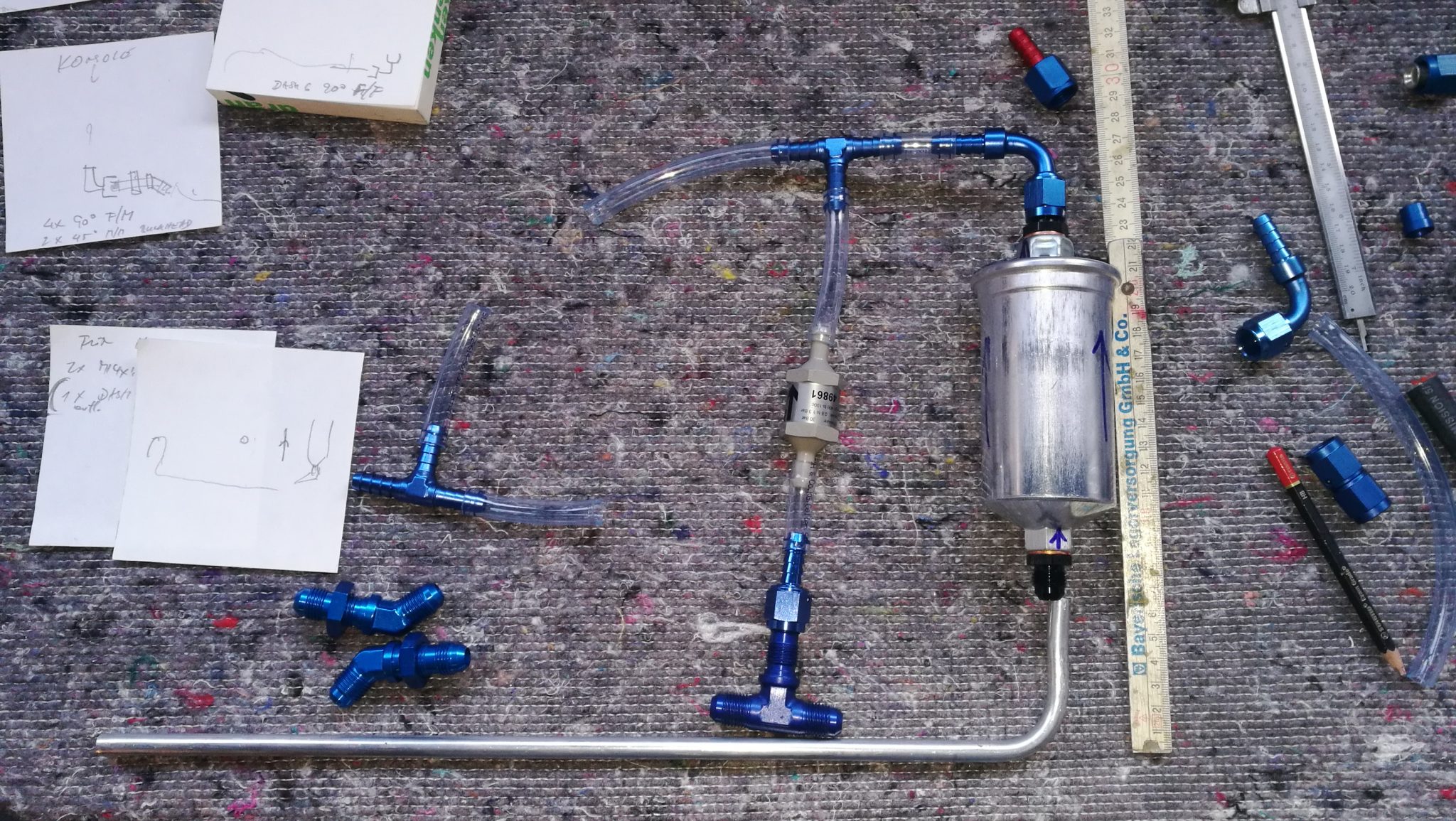
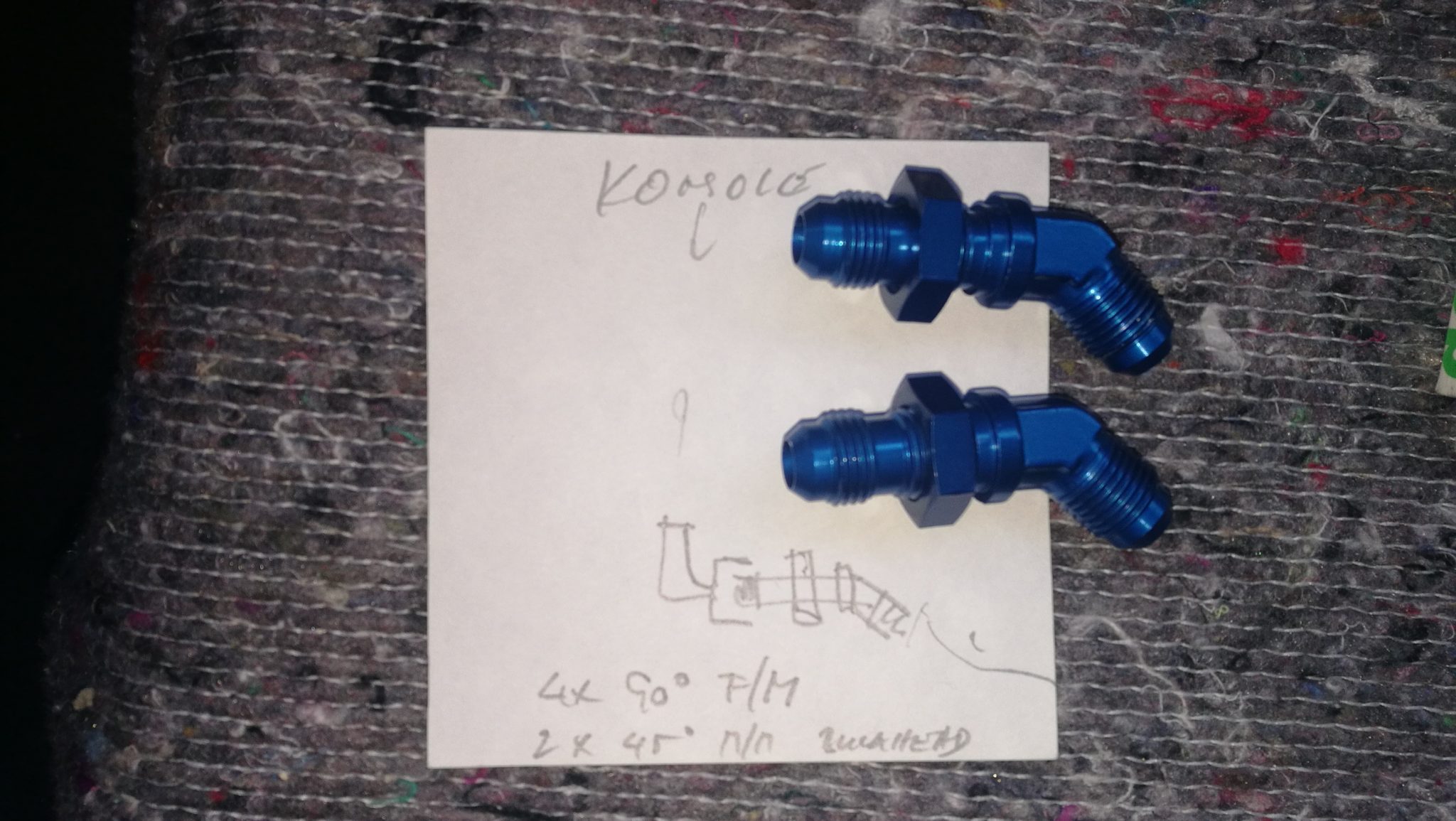